Azerbaijan Railways Prestressed Concrete Turnout Production Plant
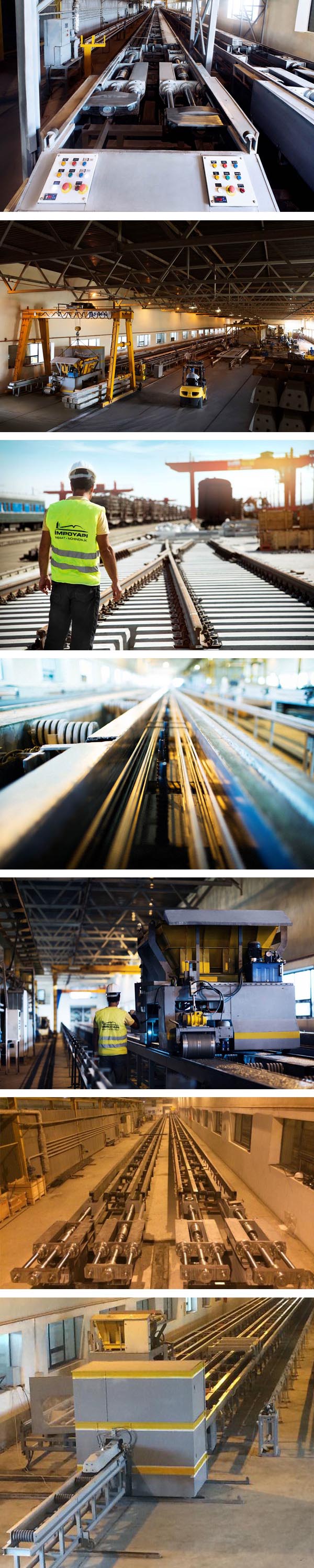
The production capacity of this facility we have built in Azerbaijan is 300 running meters per day. The system consists of four 75 meterlong production molds within 2 mainlines. It is the first and only single shear traverse production facility in Azerbaijan.
Facility Technical İnformation
PRODUCTION LINE
The two production lines have the capacity to produce 300 meter-long shear
traverses a day. Besides the hydraulic cylinders used for stretching within these
production lines, there are equipments to take the concrete in the mold out. The lifting
and turning arms included in the line are connected to a hydraulic unit and is controlled
by a panel at the end of the lines. These arms first lift the concrete block within the mold
and then turn them and leave them on the roller conveyor in the middle of the line, and
thus ready them for cutting.
STRESSİNG EQUIPMENT
Four cylinders function within the stressing process. These cylinders are
specially designed, their vertical directions intersecting with the line, and have a 300 bar
stressing force.
The hydraulic stressing process is done through the control panels at the end of the lines. With only one press of the button the equipment starts an automatic pre-stress process, and then waits for 3 minutes in order to enable the personnel to make the last controls, after which it completes the process with a final stressing procedure. During this process, the elongation of the prestressed wires are transferred to the registry panel through a device on the cylinders. These are automatically saved, thus completing the control procedure of the prestressed wire's elongation. The stressing and elongation data is saved into the on a recording device on the control panel. This way production errors are minimized, and any problem that might occur in the future will become traceable. There are 2 LCD screens on the control panel. One of these screens monitor stressing values and act as an instant dashboard, while the other instantly records processes and present them as graphics.
THE POWER SUPPLY
The equipment shown on the side picture has been specially designed for these
lines and provide power for tools that will move on the line, such as concrete casting
machines. This line is present on the whole casting line.
CONCRETE CASTİNG MACHİNE
The concrete casting machine ensures that the concrete coming from the concrete
central is poured into the mold swiftly and precisely, as well as providing concrete vibration
within the mold. There are 2 running motors on the casting machine. Also, there are 2 bottle
vibrators to ensure the vibration of the concrete cast inside the mold and a cylinder vibrator
to ensure surface smoothness after the casting. The machine can be run manually and
automatically and also has speed adjustment. Furthermore, there are external vibrators so
that there is no concrete left in the pail and so that the concrete spreads evenly. An LCD
monitor to provide automation on the machine is also present.
WİRE SHOUTİNG AND WİRE HEADİNG MACHİNE
These are some of the most important machines used in production, because as stressing
for 75 mt is done in a single procedure, it is necessary for the prestressed wire's lengths to be even
and stable. The machine provides that the prestressed wires that come in a coil are automatically
cut evenly and in the desired length, through its PLC screen. The blow molding machine ensures that
the prestressed wires connected to the stressing plaques are blown, so that they do not come about
from the plaques.
CUTTİNG MACHİNE
On the cutting machine there are censors that automatically identify the cutting
points. While automatic cutting minimizes staff errors, it is one of the main factors increasing
production speed. At the outlet of the cutting machine there are 3 compression pistons, one of
them on top and two of them on the sides. These pistons fasten the concrete block during cutting
and its vibrations prevent fractures. The cutting machine is designed so that it can operate of
future possible capacity increases and added lines. The running unit on the machine enables
switching between the lines and are fastened then they come on the processor line. The roller
conveyor on the production line can be controlled through the automation on the cutting
machine and thus the concrete block can be pulled automatically on each cutting procedure. The
PLC screen on the cutting machine enables the intervention to cutting speed, blade speed and similar processes.
WORKERS TRAİNNİNG
The assembly and startup of the system is done by our crew. In order for the facility to
operate and to be managed after the installation is completed, we provide training in critical points
about production and traverse production with our factory staff consisting of one engineer and three
from the production crew.
We also provide training in the production of concrete prescriptions, the raw materials used, in traverse cost analyses (aggregate selection, cement selection, prestressed wire technical analysis) and similar technicalities in the main activity fields of the factory. Basic training and workshops are carried out by our personnel and we take it upon ourselves that the training process is as short as possible and that production starts as soon as possible.